Bulletin #2443, Application Equipment for Potato Post-Harvest Disease Control
Developed by Steven B. Johnson, Extension Crops Specialist
For information about UMaine Extension programs and resources, visit extension.umaine.edu.
Find more of our publications and books at extension.umaine.edu/publications/.
Table of Contents:
- Background
- Equipment
- Detailed Plans and Supply List: 30-inch 4-nozzle boom, 24-inch 4-nozzle boom, 24-inch 3-nozzle boom
- Procedure
- Table 1. 40 ounces of solution per ton of potatoes
- Table 2. 48 ounces of solution per ton of potatoes
- Table 3. 64 ounces of solution per ton of potatoes
- References
Background
Late blight, caused by Phytophthora infestans (Mont.) de Bary, and pink rot, caused by Phytophthora erythroseptica Pethybr., are two devastating potato tuber diseases. These pathogens regularly cause storage losses in potato production systems. While these pathogens, especially P. infestans, spread rapidly in the field, there can also be substantial tuber-to-tuber spread during mechanical harvesting and tuber transfer procedures. With these diseases present in the field, storage losses well beyond what would be expected, based on the pathogen level in the field can occur.
Phosphorus acid (phosphonate or phosphite) is the anionic metabolite of the systemic fungicide aluminum tris-O-ethyl phosphonate (fosetyl-Al). Phosphorous acid is effective in reducing tuber-to-tuber spread of P. infestans and P. erythroseptica during mechanical harvesting and tuber transfer in a situation where the diseases are present at harvest. The mode of action of phosphorous acid is not as a nutritional source but as systemic antifungal activity towards mycelial growth.
While there are effective post-harvest treatments to control these two pathogens, the application system is a weak link. Improper application of post-harvest treatments may result in poor disease control. It is essential to calibrate application equipment precisely and apply the correct rate of material in the proper volume of the carrier. Improperly calibrated equipment can result in inadequate coverage, which can give the appearance that the treatment is ineffective when in reality, the application method is responsible.
Applications with less than half the recommended material or less than half the recommended application volume failed to provide complete control of tuber-to-tuber late blight spread. Growers tend to have zero tolerance for tuber-rot diseases in storage.
Phosphorous acid materials are generally applied at rates of 12.8 oz per ton. In Maine, growers are applying post-harvest phosphorous acid solutions ranging from 24 oz to 64 oz per ton. Unloading rates range from 15 cwt to 60 cwt per minute. With such a range in application and unloading rates, there is a need for adaptable application equipment. The equipment needs to stand up to the corrosive nature of post-harvest applied materials and be widely adaptable to varying unloading and application rates. The equipment should allow for additional nozzles and spray arms for increased flexibility.
Equipment
Growers typically use standard roller pumps, which corrode over time. The corroded pump becomes less efficient, forcing growers to recalibrate. The decaying pump also breaks down, causing both the screen and nozzle to plug. These issues cause improper applications. The use of coated roller pumps is essential, as these will last a great deal longer than the standard steel roller pumps.
Nozzle types described are TeeJet TX-2, TX-3, TX-4, or TX-6, with quick-release caps for ease of adaptability. These are brass hollow cone nozzles with an 80-degree spray pattern. The range of nozzles numbers is 3 or 4 per spray bar. Standard hydraulic couplers allow for use with any standard post-harvest applicator in use. A connector piece allows 6 or 8 nozzles to be used in higher volume situations. Nozzles need to be at a 45-degree angle, aimed forward and backward in an alternating sequence. The ideal locations for spray bars are at transition points on the bin piler where potatoes are tumbling. Unloading booms in Maine are typically 24 or 30 inches wide. For a 24-inch boom, locate nozzles 6 inches above the top of potatoes; for a 30-inch boom, locate nozzles 9 inches above the top of potatoes. Having the bin piler belt damp enhances distribution of the phosphorous acid solution on the tubers.
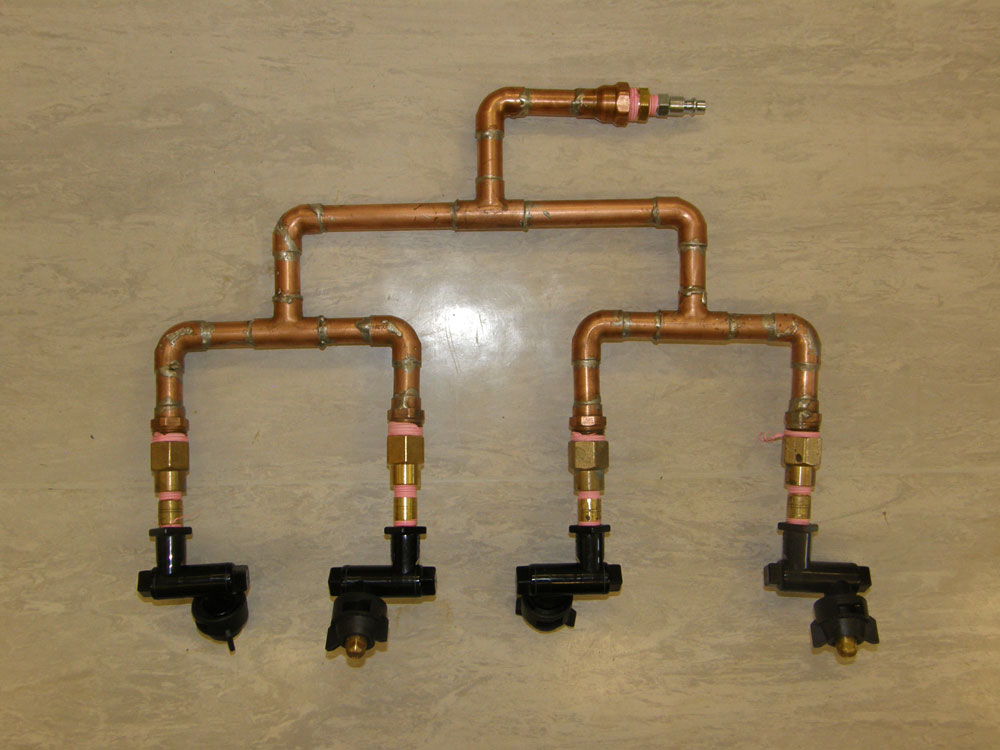
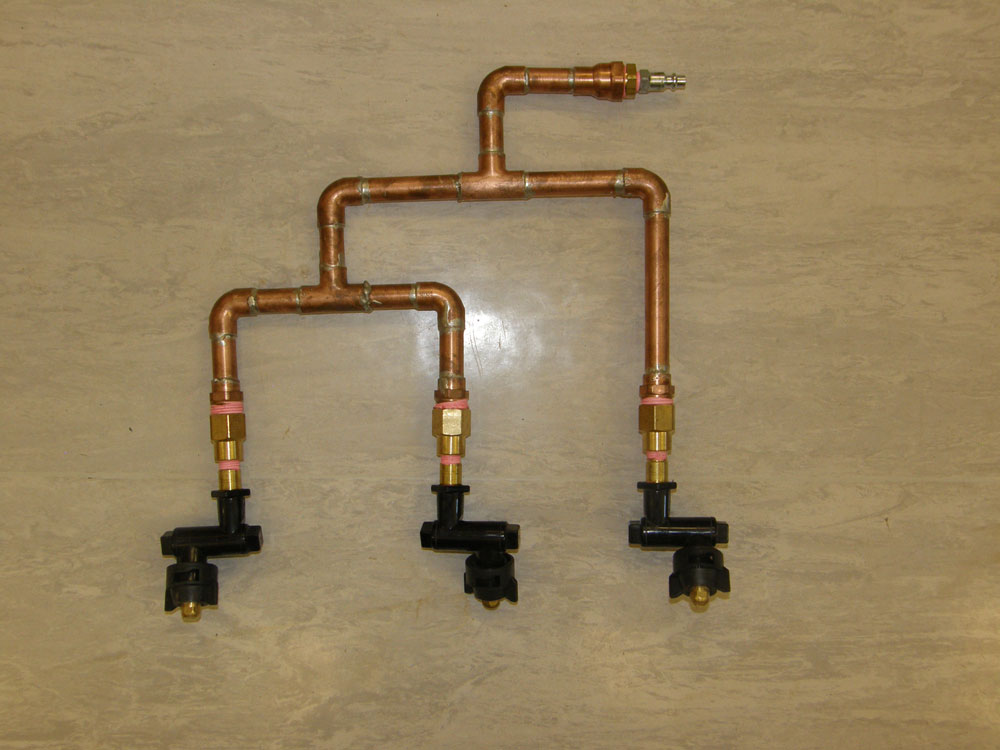
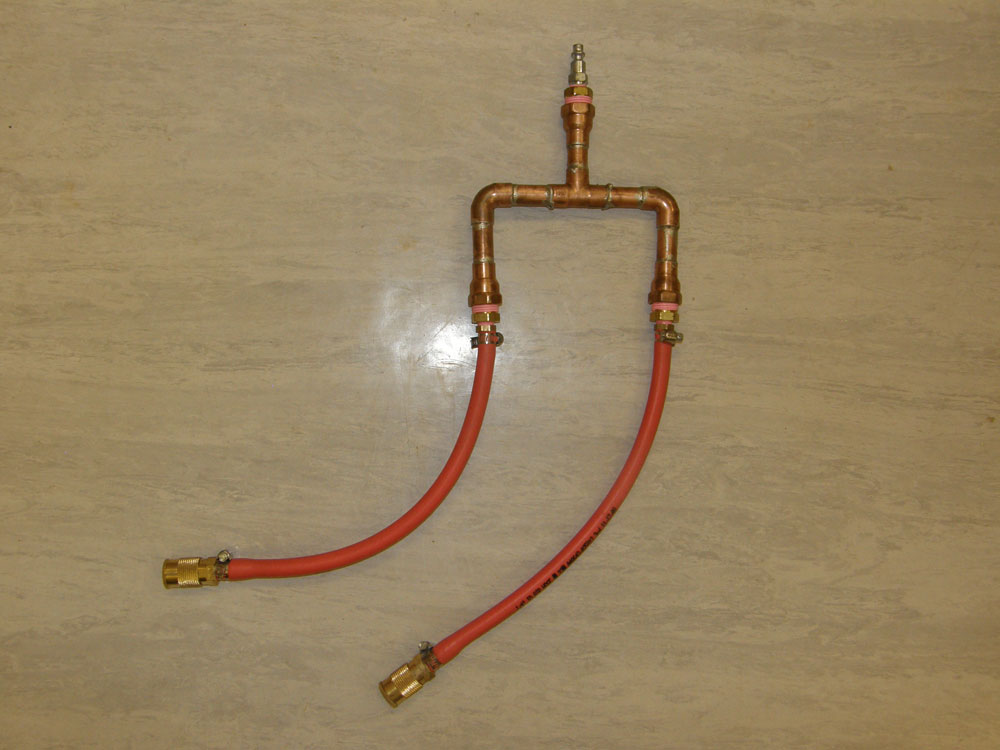
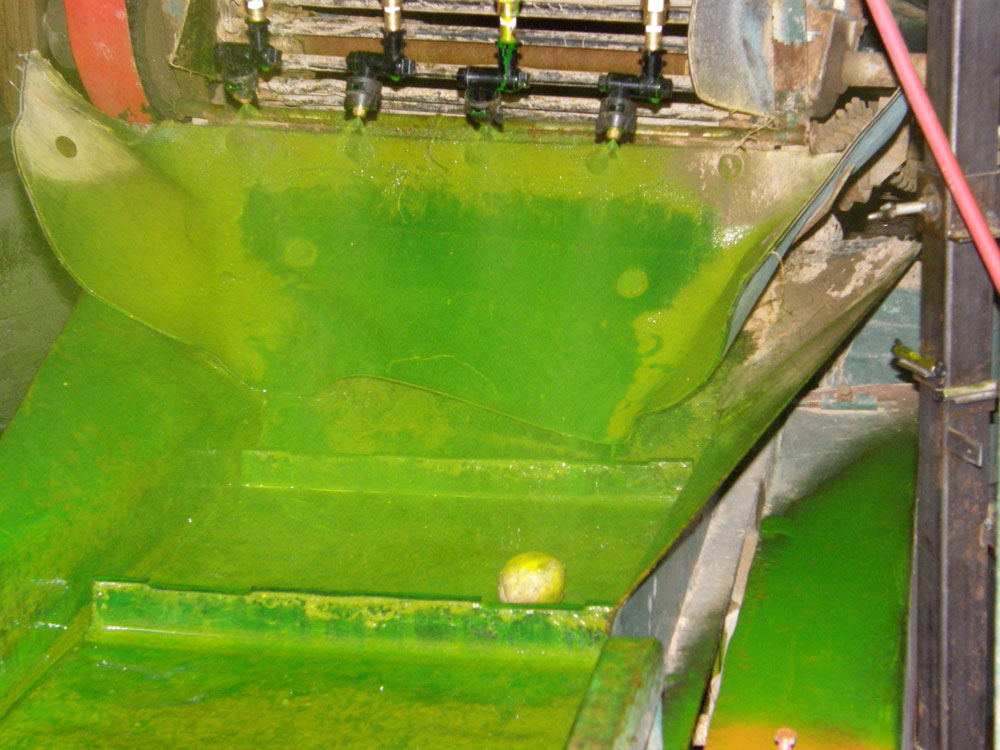
The calibration tables at the end of this bulletin provide phosphorous acid solution rates of 40, 48, and 64 ounces per ton, at 40 or 60 psi, for 3-, 4-, 6-, and 8-nozzle configurations. A three-nozzle 24-inch boom has a span of 12 inches; a four-nozzle 24-inch boom has a span of 15 inches; a four-nozzle 30-inch boom has a span of 19 inches. (Detailed Plans and Supply List below)


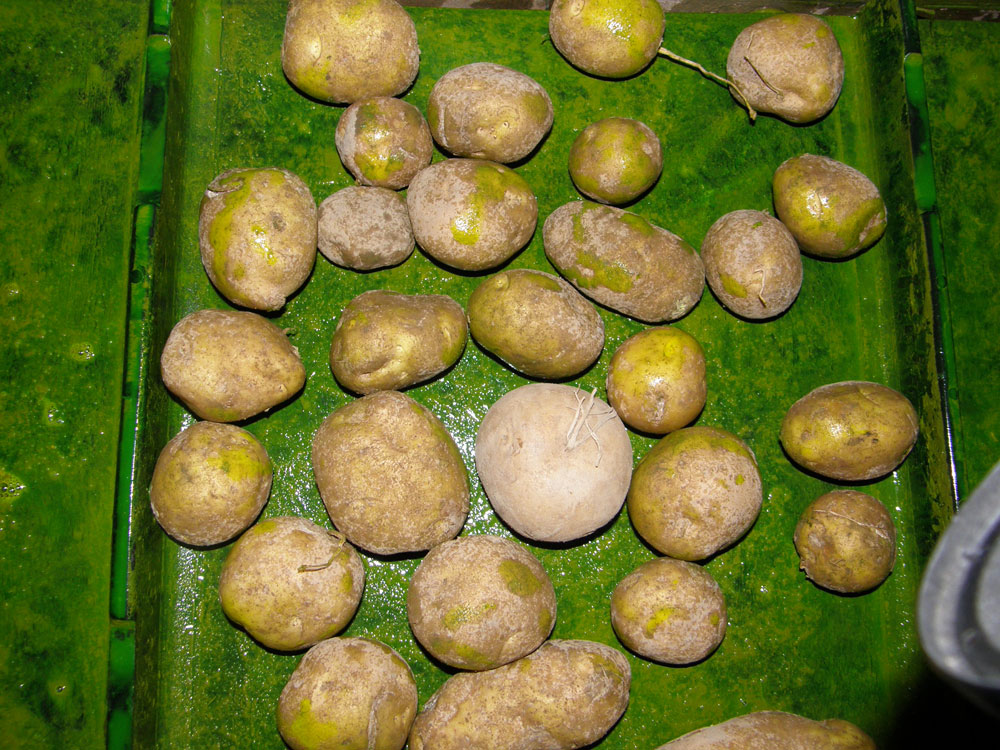
Detailed Plans and Supply List
1/2 inch PVC | 35 1/4 inches total | ![]() ![]() |
1 3/4 inch piece | 6 | |
2 3/8 inch piece | 6 | |
5 1/4 inch piece | 2 | |
1/2 inch PVC 90-degree elbow | 7 | |
1/2 inch PVC T-connector | 3 | |
1/2 inch PVC transition adaptor | 1 | |
1/2 to 1/4 inch brass bushing | 1 | |
1/4 inch brass hydraulic coupler | 1 | |
1/2 inch PVC male adapter | 4 | |
1/2 to 1/4 inch brass coupling | 4 | |
1/4 inch brass pipe nipple | 4 | |
Nozzle swivel body | 4 | |
Quick release caps | 4 |
This supply list is provided purely for educational purposes. No endorsement of products or companies is intended, nor is criticism of unnamed products or companies implied.
Procedure
- Determine the unloading rate. Timing the minutes it takes to unload a truck of known volume, and converting the truck volume into tons, will give the unloading rate in tons per minute. Convert the unloading rate in tons per minute to CWT per minute by dividing by 20. Tables 1, 2, and 3 below include unloading rates from 10 to 40 CWT per minute.
- Select the phosphorous acid solution rate. (Tables 1, 2, and 3 below include phosphorous acid solution rates of 40, 48, and 64 ounces per ton, respectively.)
- Select the application pressure. (Tables below include pressures of 40 or 60 psi.)
- Select the nozzle number on the spray bar. (Tables below include nozzle configurations of 3, 4, 6, and 8 nozzles.) Additional nozzles may be added or removed by hooking or unhooking the hydraulic connectors.
- Select the phosphorous acid rate. Consult the label of the product for the maximum rate.
The efforts of Jesse Clark and the financial support of NuFarm Americas are greatly appreciated.
References
Johnson, S. B. 2008. “Post-Harvest Applications of Phosphorous Acid Materials for Control of Phytophthora infestans and Phytophthora erythroseptica on Potatoes.” Plant Pathology Journal 7(1):50-53.
Johnson, S. B. 2010. “Post-Harvest Application of Phosphorous Acid for Control of Phytophthora infestans on Potatoes.” In: Schepers, H.T.A.M (editor): Proceedings of the Twelfth Workshop of an European Network for Development of an Integrated Control Strategy of Potato Late Blight (Arras, France, 3 – 6 May 2010). Special Report No. 14, Wageningen, the Netherlands, Applied Plant Research, Wageningen pp. 85-88.
Information in this publication is provided purely for educational purposes. No responsibility is assumed for any problems associated with the use of products or services mentioned. No endorsement of products or companies is intended, nor is criticism of unnamed products or companies implied.
© 2013, 2020
Call 800.287.0274 (in Maine), or 207.581.3188, for information on publications and program offerings from University of Maine Cooperative Extension, or visit extension.umaine.edu.
In complying with the letter and spirit of applicable laws and pursuing its own goals of diversity, the University of Maine System does not discriminate on the grounds of race, color, religion, sex, sexual orientation, transgender status, gender, gender identity or expression, ethnicity, national origin, citizenship status, familial status, ancestry, age, disability physical or mental, genetic information, or veterans or military status in employment, education, and all other programs and activities. The University provides reasonable accommodations to qualified individuals with disabilities upon request. The following person has been designated to handle inquiries regarding non-discrimination policies: Director of Institutional Equity and Title IX Services, 5713 Chadbourne Hall, Room 412, University of Maine, Orono, ME 04469-5713, 207.581.1226, TTY 711 (Maine Relay System).