Bulletin #1070, Reducing Forage Shrink and Improving Milk Production on Maine Dairy Farms
Innovative Ideas That Could Save Maine Dairy Farmers Money
Developed by Richard Kersbergen, Extension Professor, Sustainable Dairy and Forage Systems, University of Maine Cooperative Extension.
Reviewed by Gary Anderson, Animal & BioScience Specialist, Richard Brzozowski, Food System Program Administrator, Anne Lichtenwalner, DVM, Ph.D., and David Marcinkowski, Associate Professor and Dairy Specialist, University of Maine Cooperative Extension.
For information about UMaine Extension programs and resources, visit extension.umaine.edu.
Find more of our publications and books at extension.umaine.edu/publications/.
Forage production is the biggest operating expense for most dairy farms, and quality forage production is the basis of a high producing dairy ration. Harvesting forage is expensive and farmers can experience considerable nutrient loss anytime along the process from planting to harvest and storage and feeding.
One of the goals of a well-managed forage program should be to minimize losses during the chain of events from harvest to feeding. Once the feed is cut, the quality and quantity of the forage begin to decline. Controlling the losses along the way is important for controlling volume but also the milk-producing potential of the forage being fed.
All dairy farms in Maine experience forage shrink. Some shrink is inevitable. In the field, losses in haylage production occur as soon as the forage is mowed, with respiration losses quickly reducing the quality of the forage. Wide swath mowing with rapid drying has helped to reduce respiration losses and also reduce weather exposure risk. This technique should be part of all farms’ Standard Operating Procedures (SOP) for quality forage.
Packing and covering bunkers is another area of forage production where shrinkage can be reduced. Estimates are that dairy producers lose up to to 30% due to shrink and poor management once the feed gets to the bunker. Using a case study from the University of Minnesota, an average 100-cow dairy farm can save $2,500 by simply reducing storage and feed-out shrink by just 5% (Pepin, University of Minnesota, 2015).
Packing the bunker to achieve a high density of the material is critical to enabling good fermentation and preservation of nutrients. Often overlooked, the management of feed going into the bunker is often a weak link in production. Each load being delivered should be distributed over the pile and packed to achieve a density of 15 to 17 lbs./DM per cubic foot. Packing consistently and slowly helps to achieve that goal. Additional weights and tools can aid in packing density to improve fermentation and reduce losses.
Shrink also can be reduced when covering the pile. If you have done a good job harvesting and packing, you need to protect your investment by covering well. This means considering using an oxygen barrier plastic under the regular silage plastic. One sheet of oxygen plastic is equivalent to 60 sheets of regular silage plastic cover. Most oxygen barriers are thin, so they will need a 5-6 mil regular plastic cover on top. Finally, seal the top well with wall to wall tires and seal the edges with bags of sand or pea stone to minimize both water and air infiltration.
Feedout is a huge area of loss as well. Minimizing the amount of bunker face exposed to air is critical to feeding fresh feed to your cows. How you remove the feed can influence the quality and consistency of forage. Recently, some producers in Maine have been using “facers” to remove the feed from silos. These units “rake” the face of the silo in a downward motion, minimizing the amount of air that gets into the silo as compared to a bucket loader or skid steer, where often the feed is removed with an upward motion of the bucket, allowing oxygen into the bunker and beginning the deterioration of the next day’s feed. Once exposed to oxygen, your silage quickly begins the change from quality feed to warm compost as it heats up and quickly degrades.
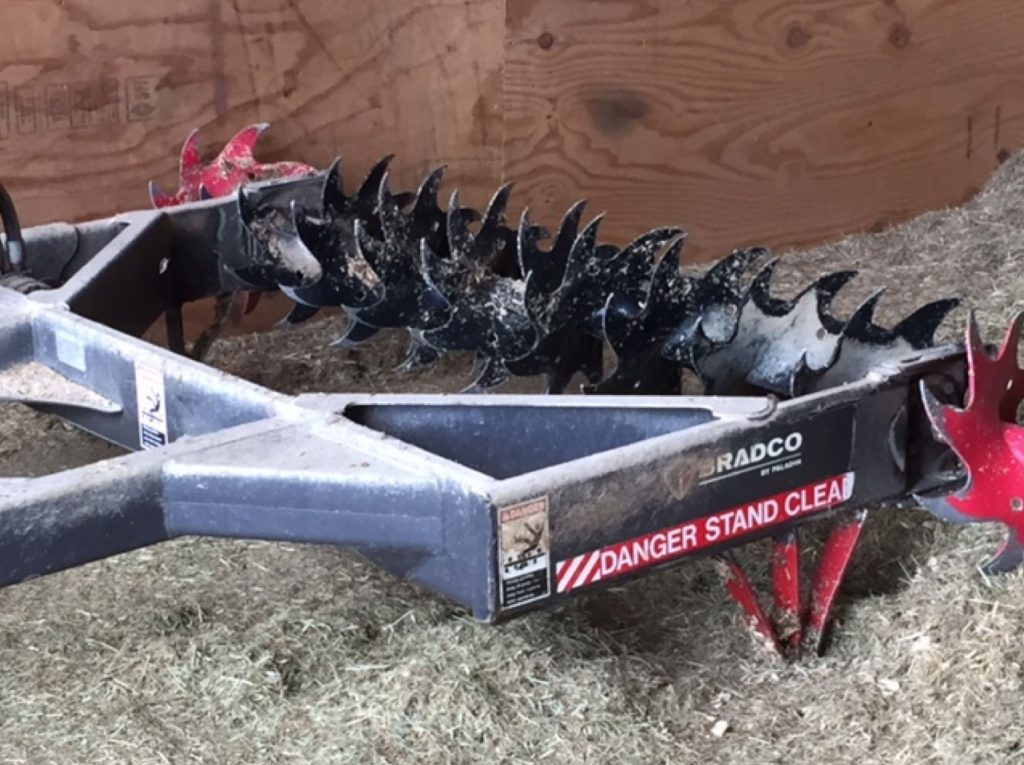
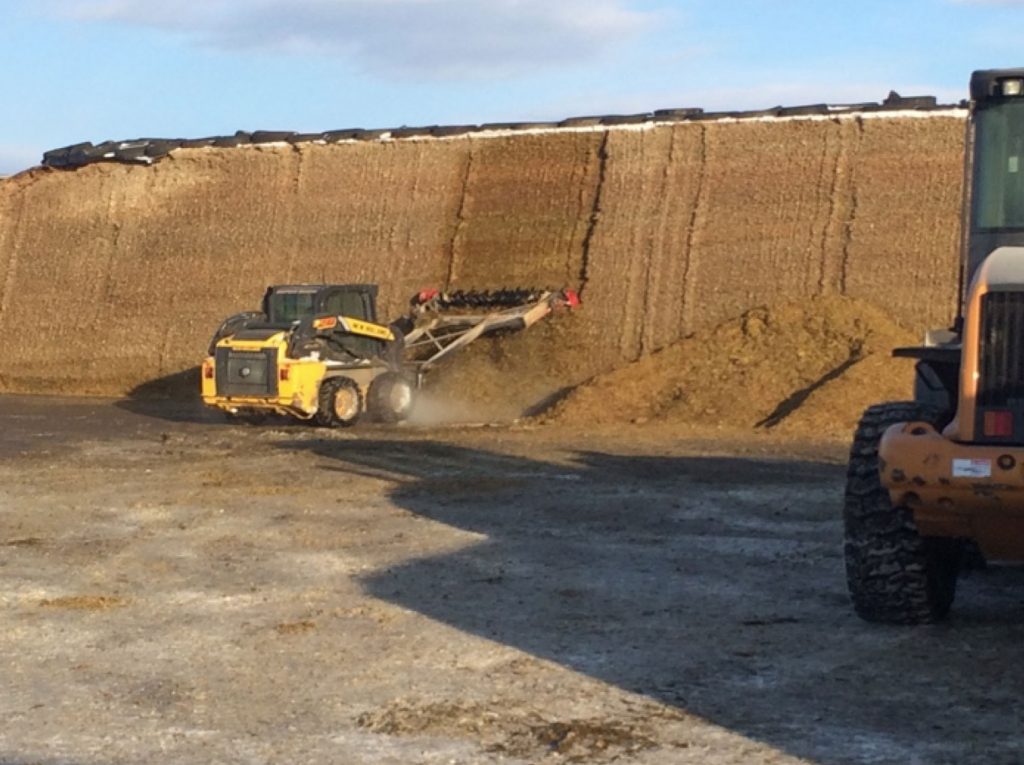
Some quick surveys of producers who now use facers have produced the following statements:
- “Once we started using a facer, we gained nearly 3 lbs. of milk per cow and the unit payback was within 3 months on our 400-cow dairy.”
- “By using a facer, we have significantly reduced the amount of feed we discard from the feed bunk.”
- “Before using the defacer, our daily milk production used to vary considerably from pick-up to pick-up. Now our production is much more consistent, and we have almost no waste!”
Most facers are implements that are driven hydraulically and attach to a skid steer or bucket. They range in cost from about $4,000 to $8,000. Some producers in Maine have constructed their own with materials from around the farm.
Another benefit of using a facer, along with reducing shrink and loss from the silo, is the elimination of big chunks of silage that don’t blend well in the mixer wagon, especially during winter. Better blended forage will also reduce sorting of the TMR. One drawback may be an increase in the time required for feeding, as the feed will first need to be scraped and then loaded into the wagon. This would be especially true if the same equipment was used for facing as well as loading.
The University of Wisconsin (Team Forage Division of Extension) has a spreadsheet that helps determine the breakeven costs, at the bottom of the web page.
The Maine Dairy Improvement Fund (MDIF) was recently made available to Maine dairy farmers. If you use a bunker silo for your forages, implementing some of the techniques discussed in this article and using MDIF as a resource, the purchase of a facer might easily produce an increase in revenue for your farm.
For more information about the MDIF, visit the Agricultural Resource Development Division, Dairy Improvement Fund (Maine.gov Department of Agriculture, Conservation and Forestry website).
Additional Resources
University of Maine Cooperative Extension (county office contacts, books, and publications).
Information in this publication is provided purely for educational purposes. No responsibility is assumed for any problems associated with the use of products or services mentioned. No endorsement of products or companies is intended, nor is criticism of unnamed products or companies implied.
© 2018
Call 800.287.0274 (in Maine), or 207.581.3188, for information on publications and program offerings from University of Maine Cooperative Extension, or visit extension.umaine.edu.
In complying with the letter and spirit of applicable laws and pursuing its own goals of diversity, the University of Maine System does not discriminate on the grounds of race, color, religion, sex, sexual orientation, transgender status, gender, gender identity or expression, ethnicity, national origin, citizenship status, familial status, ancestry, age, disability physical or mental, genetic information, or veterans or military status in employment, education, and all other programs and activities. The University provides reasonable accommodations to qualified individuals with disabilities upon request. The following person has been designated to handle inquiries regarding non-discrimination policies: Director of Equal Opportunity and Title IX Services, 5713 Chadbourne Hall, Room 412, University of Maine, Orono, ME 04469-5713, 207.581.1226, TTY 711 (Maine Relay System).