Respirators and Pesticides II: Fit-Testing and Other Respirator Requirements for Occupational Use
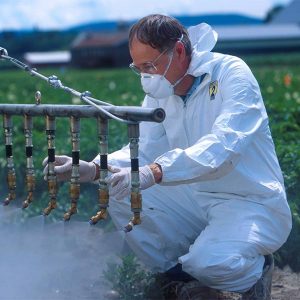
Prepared by Kerry Bernard, Pesticide Safety Education Professional
Reviewed by Jason Lilley, Sustainable Agriculture Professional, and Jim Dill, Pest Management Specialist
UMaine Cooperative Extension Diagnostic and Research Laboratory, Pest Management Unit, 17 Godfrey Drive, Orono, ME 04473-3692, 207.581.3880 extension.diagnosticlab@maine.edu
Occupational Respirator Use
The occupational use of respirators for pesticides is regulated by the EPA’s Worker Protection Standard (WPS) in agricultural settings and OSHA’s Respiratory Protection Standard (RPS) in other settings. Before an individual wears a respirator for work, both protection standards require them to complete:
- a medical evaluation,
- fit-testing, and
- respirator training
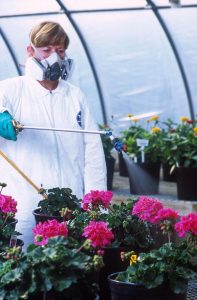
The standards also require fit-checks with each use; recordkeeping; proper use, storage, and maintenance of respirators; and the RPS requires a written plan for respiratory protection.
Medical Evaluations
Breathing through non-powered, air-purifying respirators (APRs) is more strenuous than normal breathing. Those with certain respiratory, cardiovascular, and other medical conditions may not be able to do so without risk to their health. Even supplied-air respirators (SARs) and powered air-purifying respirators (PAPRs) may be unsafe for some, due to the weight of the equipment and other factors. Therefore, medical evaluations are required:
- For users of ALL respirators
- Before using a respirator
- Initially, and whenever
- the user’s health changes,
- recommended by a Physician or other Licensed Health-Care Professional (PLHCP),
- the work becomes more strenuous,
- using a respirator becomes difficult for the user, or
- mandated in Maine’s public sector
- Before fit-testing
- To be performed by a PLHCP, either
- online via Respirator Medical Evaluation Questionnaire, or
- in person at an occupational health center or regular doctor’s office
- To be paid for by the user’s employer
Medical information is confidential, so only the PLHCP’s determination may be viewed by the employer, not answers to the questionnaire evaluation.
Fit-Testing
Variation in the size, structure, and features of individuals’ faces means that not everyone can get a seal with the same respirator. And without a proper seal, a tight-fitting respirator will not protect against pesticides. Employers should provide a range of respirator makes, models, styles, and sizes for fit-testing so users can find one that will work for them.
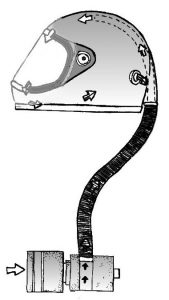
Fit-testing is required:
- Before using a respirator
- For ALL tight-fitting respirators, including filtering facepieces
- Annually, and whenever
- the user switches to a
- make, model, style, or size of
- respirator they haven’t been fit-
- tested with that year, or
- the user’s face has changed
(new scars, dentures, facial surgery, significant weight change, etc.).
Loose-fitting PAPRs (pictured right) do not require fit-testing and present an alternative for individuals who can’t pass a fit-test with a tight-fitting respirator.
There are two types of fit-tests:
- Qualitative — A pass/fail test in which the user dons the respirator and tries to detect banana oil (for respirators with an organic vapor or combo cartridge/canister), or Bitrex™ or saccharin aerosol (respirators with a particulate filter or combo cartridge/canister). These tests can be performed with relatively cheap materials, by ANYONE who can follow the protocols. Some respirator manufacturers sell qualitative fit- test ‘kits’, which include the necessary materials and protocols. Full protocols are also described in OSHA 1910.134 Appendix A and the Pesticide Educational Research Collaborative’s (PERC’s) WPS Respiratory Protection Guide.
- Quantitative — A test administered by a specially trained individual that determines the amount of leakage, and calculates a respirator’s ‘fit-factor’ based on measurements taken inside the facepiece.
For more information on fit-testing, visit the Occupational Safety and Health Administration’s Respiratory Fit Testing (Pruebas de Ajuste de los Respiradores) page ( United States Department of Labor)
Where to get fit-tested in Maine
- Concentra — Augusta, Bangor, Lewiston, Norway
- Health Screening USA — North Windham
- Life Safety Specialists, Inc. — Norway
- Northern Light’s Work Health — Bangor, Portland, Presque Isle, Waterville
- Southern Maine Health Care’s WorkWell program — Biddeford, Sanford
- St. Joseph’s WorkWell — Bangor
- Mobile health and occupational safety clinics
- Anywhere (qualitative), with the materials, protocols, and a competent helper
Respirator Training
Employers must provide annual respirator training to all employees who use pesticides with a respirator requirement on the label. After the training, employees must be able to demonstrate their understanding of
- the importance of respirators,
- the limitations of respirators,
- respirator and cartridge/canister selection and replacement,
- respirator use in an emergency and what to do if a respirator fails,
- how to wear and remove a respirator correctly and how to perform fit checks,
- respirator inspection, maintenance, storage, and
- how to recognize medical symptoms that may limit the effective use of a respirator.
Individuals to whom the RPS applies must also complete worksite specific training.
Self-employed individuals may train themselves if they can do so thoroughly and keep good records.
Fit-Check
Each time a user puts on a tight-fitting respirator, they must conduct a fit/seal-check to ensure that the respirator is positioned properly, with an uninterrupted seal between the respirator and skin. Otherwise, contaminants could leak inside the mask. There are two types of fit-checks:
- Positive-pressure check – Block the exhalation valve with a palm, then exhale. For filtering facepieces without a valve, block the entire facepiece with both hands, then exhale.
The facepiece should feel like it’s bulging slightly. If air escapes beneath the facepiece, there is no seal and the respirator must be repositioned until one can be achieved.
- Negative-pressure check – Block the inhalation valves/cartridges with both palms, inhale, and hold for 10 seconds.
The facepiece should collapse. If it expands before exhalation, reposition and re-check.
Planning and Recordkeeping
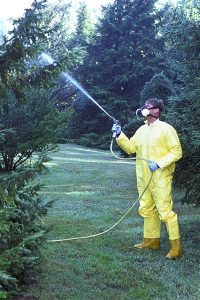
Respirators should be the last line of defense. Whenever reasonable, eliminate situations that put respiratory health at risk through planning and engineering controls. Consider substituting products that require a respirator for those that don’t.
OSHA specifically requires pest control companies to design and implement a written Respiratory Protection Plan (RPP) and the designation of a program administrator. Though not mandated by the WPS, it’s always a good idea to institute a respirator program and put one person in charge of it.
Records need to be kept of medical determinations, fit-tests, and training. Under the WPS each must be kept for 2 years. Under the RPS, medical determinations must be kept for the duration of employment, plus 30 years. Fit-test records must be kept for one year—until the next fit-test. Past training does not have to be documented, but current training plans need to be included in the written RPP.
Other Requirements
Employers are responsible for ensuring their employees use the right respirator(s) for the work, use them correctly, and that the respirators are maintained and stored properly. Specifically, respirators must be:
- used according to manufacturer instructions,
- inspected for worn, torn, and broken parts, and re-paired,
- cleaned and dried prior to each day of reuse,
- stored away from pesticides, contaminated areas, and personal items,
- handled with gloves prior to cleaning, if contaminated (and the product requires gloves),
- left at work, if contaminated,
- used in accordance with a change-out schedule, depending on the type of respirator, the conditions, the manufacturer’s instructions, and other factors.
All but the last point applies to all other PPE as well.
This material is meant as a general guide only. Always follow pesticide label and respirator manufacturer instructions.
For more information on respirators and their use, see:
- NIOSH/CDC: cdc.gov/niosh, Email: cdc-info@cdc.gov, 800.232.4636
- OSHA: osha.gov, 800.321.6742
- EPA: epa.gov/pesticides, Email: pesticidequestions@epa.gov
- PERC: pesticideresources.org
- AgriSafe Network: agrisafe.org/lungs-for-life
- Maine BPC: thinkfirstspraylast.org, 207.287.2731
- UMaine Extension Professionals: Jason Lilley, jason.lilley@maine.edu, 207.781.6099, or Kerry Bernard, kerry.bernard@maine.edu, 207.581.3884
To download and print this brochure:
Disclaimer
Pesticide safety information may change over time. This information is provided for educational purposes only and was published in 2019.
Although pesticides can be an essential tool in pest management, the improper use and disposal of these chemicals present a continuing risk to humans, animals, and the environment. It’s important for applicators to understand that pesticide safety is not only about protecting themselves — it’s also about protecting our domestic and wild animals, the environment, our landscapes, and our communities.
Misuse of pesticides can result in, or contribute to, serious injury, illness, or death. Cooperative Extension does not guarantee the safety or effectiveness of any product or practice. Users of any pesticides, and Extension’s educational materials, do so at their sole risk and assume all risk from using such pesticides and materials, whether they follow recommendations or not. The user bears all responsibility for resulting damages to property, human health, or the environment. Cooperative Extension and the University of Maine System shall not be responsible for any damages including, but not limited to, any and all damage or loss to real or personal property, personal injury or death, resulting from the negligence of cooperative extension, the university, its trustees, faculty, agents, employees or volunteers.
Always follow directions on pesticide labels! Failure to do so violates federal law. Application timing and proper calibration are as important as using the right product.
Cooperative Extension makes no warranty or guarantee of any kind, expressed or implied, concerning the use of any stated products. Trade names are used for identification only; no product endorsement is implied, nor is discrimination intended.
Source material includes publications from EPA, CDC/ NIOSH, OSHA, Oregon OSHA, and PERC, and Cooperative Extension Offices from Pennsylvania State University, Rutgers University, University of Florida, and the University of Nebraska. Photos courtesy of USDA-ARS. Illustrations by Donald Barry.
The University of Maine is an EEO/AA employer and does not discriminate on the grounds of race, color, religion, sex, sexual orientation, transgender status, gender expression, national origin, citizenship status, age, disability, genetic information or veteran’s status in employment, education, and all other programs and activities. The following person has been designated to handle inquiries regarding non-discrimination policies: Director of Equal Opportunity, 101 North Stevens Hall, University of Maine, Orono, ME 04469-5754, 207.581.1226, TTY 711 (Maine Relay System).