Respirators and Pesticides III: Proper Respirator Use and Maintenance
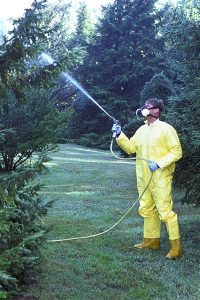
Prepared by Kerry Bernard, Pesticide Safety Education Professional
Reviewed by Jason Lilley, Sustainable Agriculture Professional, and Jim Dill, Pest Management Specialist
UMaine Cooperative Extension Diagnostic and Research Laboratory, Pest Management Unit, 17 Godfrey Drive, Orono, ME 04473-3692, 207.581.3880 extension.diagnosticlab@maine.edu
Using and Maintaining Respirators Properly
When properly used and maintained, respirators can protect the respiratory system from pesticide exposure, preventing serious medical harm or even death. If used incorrectly or improperly maintained, however, they offer only a false sense of security. Respirators themselves may even pose a health risk to certain individuals.
That’s why it’s important to get medical clearance before wearing a respirator, to make sure it’s the right respirator for the job, and to use the only respirator makes, models, styles, and sizes for which one has been fit-tested and trained to use. It’s also critical to read and follow the respirator manufacturer’s directions and the pesticide label.
Selection
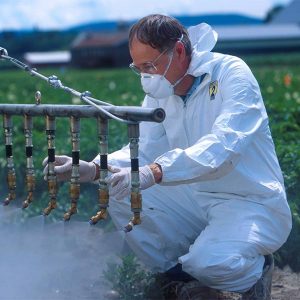
Different respirators are necessary for different pesticides and concentrations. A respirator less protective than those listed on the label will not prevent all — if any — exposure. Neither will be using the wrong filter, cartridge, or canister.
Always refer to the label of the specific pesticide product being used to determine which respirators, filters, and cartridges are acceptable.
When in doubt, consult a respirator manufacturer to help find the right respirator for the situation. Always read the respirator manufacturer’s instructions carefully before wearing a new respirator.
For information on the different types of respirators, their uses, filters and cartridges, and how to interpret outdated respirator language, see Respirators and Pesticides I.
Wearing the Respirator
Always inspect a respirator before putting it on. Check for:
-
— Photo courtesy of USDA-ARS Cleanliness — if it hasn’t been cleaned since its last use, clean it.
- Distortion of the facepiece.
- Stretched straps.
- Check valves, diaphragms, fittings, gaskets, and tubing for cracks, wear, tears, and deterioration.
- If using a powered air-purifying respirator (PAPR), check the batteries and any alarm or indicator lights.
Put on the respirator before any head coverings or eye-wear—nothing can go between a tight-fitting respirator and the head and face. Glasses, goggles, scarves, jacket hoods, hats, etc. go on over the respirator. For individuals who need glasses and wear a full-face respirator, manufacturers make spectacle kits in which prescription lenses can be set.
When wearing a respirator, one set of straps should rest above the ears and one below. Make sure the respirator is seated properly on the face and that no hair or anything else comes be-tween the facepiece and skin. If using a filtering facepiece, carefully shape the nose clip by pressing it down around the nose with both hands, don’t just pinch it.
Facial hair that crosses between the facepiece of a tight-fitting respirator and the skin will prevent a good seal. Individuals with beards or most other styles of facial hair cannot wear them safely. Either they will have to shave clean or wear a loose-fitting respirator. This leaves only PAPRs and atmosphere-supplying respirators as options. These offer better protection than nonpowered air-purifying respirators, but they’re much more expensive and can be cumbersome.
Users must successfully complete a positive-pressure or negative-pressure fit-check (both is better) every time they wear a tight-fitting respirator. This ensures that the respirator is sealed against the face and not leaking.
To perform a positive-pressure check:
- Block the exhalation valve with a palm, then exhale. For filtering facepieces without a valve, block the entire facepiece with both hands, then exhale.
The facepiece should bulge slightly without air escaping. To perform a negative-pressure check:
- Block the inhalation valves/cartridges with both palms, inhale, and hold for 10 seconds.
The facepiece should collapse. If it expands before exhalation, reposition and re-check.
When using the respirator:
- Know how long the filters/cartridges/battery should last and leave the contaminated area before they stop working.
- Beware of heat stress. The added strain of breathing through a non-powered APR can increase the risk of heat-related illness. Workaround hot weather, if necessary.
- If the pesticide is smelled or tasted through the respirator, leave the contaminated area at once.
- If feeling ill or having trouble breathing, stop work and get to fresh air immediately.
Don’t take off the respirator until back in a non-hazardous atmosphere, even if it seems to be leaking. Avoid cross-contamination during removal—don’t touch a contaminated respirator without gloves or set it where it will contaminate clean areas/materials.
Change-Out Schedule
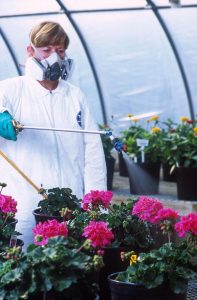
Disposable respirators, filters, cartridges, and canisters, have finite service lives, beyond which they cannot adequately protect the user. The length of service life depends upon
- the type of component,
- brand,
- pesticide(s) being used,
- pesticide formulation,
- pesticide concentration,
- time removed from original packaging,
- breathing rate of the wearer, and
- temperature, humidity, and other environmental factors.
Don’t assume cartridges last until the pesticide is detected by the user. Individuals vary in their ability to taste and smell chemicals, and some pesticides can cause serious harm in concentrations lower than some individuals can sense. Manufacturer directions usually specify how long a cartridge/canister/filter is good for under certain conditions. Some cartridges and canisters have end-of-service-life indicators (ESLIs), which change color as the ESL nears. And many PAPRs have alarms or lights that go off when the filter or battery needs to be changed.
It’s always a good idea to establish a documented change-out schedule, and OSHA requires it of employers. These can be created using
- the manufacturer’s directions,
- software from NIOSH or the respirator manufacturer that can calculate an estimate of a product’s ESL for very specific conditions, or
- the results of experiments conducted under the specific conditions
Always adhere to the established schedule, or in the absence of one, the manufacturer’s instructions. In general, filters/cartridges/canisters shouldn’t be used for more than one 8-hour shift. These components can’t be cleaned and organic vapors adsorbed in a cartridge or canister can release over time. If a filter/cartridge/canister is designed for use beyond a single work period,
- keep a log of its use,
- record the date, time used, and cumulative time used, for each use,
- write the cumulative time used on the bag the cartridge is stored in, and
- replace the cartridge before the cumulative time used exceeds the time indicated by the change-out schedule.
Always check the date on new cartridges/canisters before installing them—they expire.
Replace filters when they become difficult to breathe through, if they become damaged if they get wet, or in the case of an R-class filter, by 8-hours of use.
Cartridges/canisters/filters aren’t interchangeable between brands—use only those designed for the respirator make and model.
Cleaning and Maintenance
Keeping respirators clean is important because:
- a contaminated respirator can be a source of pesticide exposure,
- a dirty respirator may not seal against the skin, and
- a moldy respirator presents its own respiratory hazards.
Always clean the respirator before the next use (preferably before storage), according to the manufacturer’s directions.
The following steps should be followed in the absence of manufacturer directions:
- Disassemble and inspect the parts of the respirator.
- Discard spent cartridges, filters, and any broken or worn parts. Replace bad parts before the next use, using only parts designed for the specific make, model, and style of the respirator.
- Wash respirator parts in warm water with a mild detergent, scrubbing gently.
- Disinfect as needed.
- Dry thoroughly before storing it.
Ideally, each individual required to use a respirator would have their own. If however, a respirator must be shared, disinfect it before the next person uses it, following the manufacturer’s directions. If none are given, soak the respirator parts for 2 minutes in 2 tablespoons of bleach per gallon of water solution. Rinse and dry thoroughly. Do not share filtering facepiece respirators, they can’t be cleaned.
Storage
Store clean, dry respirators in clean, dry containers/bags with some ventilation. Do not store them in areas contaminated by pesticides or other chemicals. Keep them out of direct sunlight and extreme temperatures. Avoid com-pressing during storage as it can distort the shape of the facepiece and other parts. Do not take respirators home from work. Store partially used filters/cartridges/canisters in airtight containers, separate from respirators.
Put Someone in Charge
Where multiple people are using respirators, designating a responsible individual to keep track of respirator issues can avoid problems. This person can maintain the records of medical exams, fit-testing, and training, making sure everyone is up-to-date. They can also ensure that the change-out schedule log is being filled out and that new filters/cartridges/canisters are available. Lastly, they can check that the respirators are being maintained and stored correctly.
Know the Limitations
Understand that respirators are only protective so long as they’re used correctly. An ill-fitting respirator is not useful, neither is a respirator with spent cartridges or filters. And remember, a respirator can only do what it’s been designed to do:
- APRs cannot add oxygen to a deficient atmosphere. Do not use them when oxygen levels are below 19.5%.
- Particulate filters cannot prevent gas or vapors from passing into the facepiece.
- The sorbants in chemical cartridges cannot bind particulates.
- One chemical cartridge or canister can’t adsorb all contaminants — each only protects against certain types of gases/vapors.
- Air can be too contaminated for an APR to purify — never wear an APR where the contaminant or the contaminant concentration is unknown. Use a SAR.
When There’s a Problem
Respirators can fail, often due to a poor fit/seal or a contaminant exceeding the filter’s/cartridge’s/canister’s ability to purify the air. They can also put a lot of strain on the body, especially in hot weather. Individuals must stop work and get to fresh air immediately if they experience any of the following, regardless of the cause:
- The smell or taste of chemicals
- Irritation of the nose and/or throat
- Difficulty breathing
- Weakness
- Dizziness
- Tightness in the chest
- The feeling that the breathed air is too o warm
- Nausea
- Confusion
- Sleepiness
This material is meant as a general guide only. ALWAYS follow pesticide label and respirator manufacturer instructions. For more information on respirators and their use, see:
- NIOSH/CDC: cdc.gov/niosh, Email: cdc-info@cdc.gov, 800.232.4636
- OSHA: osha.gov, 800.321.6742
- EPA: epa.gov/pesticides, Email: pesticidequestions@epa.gov
- PERC: pesticideresources.org
- AgriSafe Network: agrisafe.org/lungs-for-life
- Maine BPC: thinkfirstspraylast.org, 207.287.2731
- UMaine Extension Professionals: Jason Lilley, jason.lilley@maine.edu, 207.781.6099, or Kerry Bernard, kerry.bernard@maine.edu, 207.581.3884
To download and print this brochure:
Disclaimer
Pesticide safety information may change over time. This information is provided for educational purposes only and was published in 2019.
Although pesticides can be an essential tool in pest management, the improper use and disposal of these chemicals present a continuing risk to humans, animals, and the environment. It’s important for applicators to understand that pesticide safety is not only about protecting themselves — it’s also about protecting our domestic and wild animals, the environment, our landscapes, and our communities.
Misuse of pesticides can result in, or contribute to, serious injury, illness, or death. Cooperative Extension does not guarantee the safety or effectiveness of any product or practice. Users of any pesticides, and Extension’s educational materials, do so at their sole risk and assume all risk from using such pesticides and materials, whether they follow recommendations or not. The user bears all responsibility for resulting damages to property, human health, or the environment. Cooperative Extension and the University of Maine System shall not be responsible for any damages including, but not limited to, any and all damage or loss to real or personal property, personal injury or death, resulting from the negligence of cooperative extension, the university, its trustees, faculty, agents, employees or volunteers.
Always follow directions on pesticide labels! Failure to do so violates federal law. Application timing and proper calibration are as important as using the right product.
Cooperative Extension makes no warranty or guarantee of any kind, expressed or implied, concerning the use of any stated products. Trade names are used for identification only; no product endorsement is implied, nor is discrimination intended.
Source material includes publications from EPA, CDC/ NIOSH, OSHA, Oregon OSHA, and PERC, and Cooperative Extension Offices from Pennsylvania State University, Rutgers University, University of Florida, and the University of Nebraska. Photos courtesy of USDA-ARS.
The University of Maine is an EEO/AA employer and does not discriminate on the grounds of race, color, religion, sex, sexual orientation, transgender status, gender expression, national origin, citizenship status, age, disability, genetic information or veteran’s status in employment, education, and all other programs and activities. The following person has been designated to handle inquiries regarding non-discrimination policies: Director of Equal Opportunity, 101 North Stevens Hall, University of Maine, Orono, ME 04469-5754, 207.581.1226, TTY 711 (Maine Relay System).